Computex 2014 In Win Factory Tour
Author: Dennis GarciaIntroduction
One of the first cases I ever bought was an In Win design. Sure it was beige and offered no frills but the case was built like a tank from quality SECC steel and used a combination of rivet and spot welds to hold it together. This year before Computex I was invited, along with some other media, to take an exclusive tour of the In Win factory and see what it takes to assemble a case, start to finish.
I'm no stranger to manufacturing and am familiar with many of the machines required to so plastic injection and metal stamping but seeing them in action is something you must experience in person if you ever want to fully understand how they work.
Manufacturing facilities are configured based on what they are building. In the case of the In Win factory the majority of the factory floor is dedicated to metal stamping to create the various parts of a computer case. The metal presses themselves are configured in an assembly line format with actual humans at each end. At the start is a flat piece of SECC steel that is lifted to the line using a robot arm and suction cups. Once the metal is dropped on the line a conveyor pushes the metal thru a series of presses so it can take on the required shape.
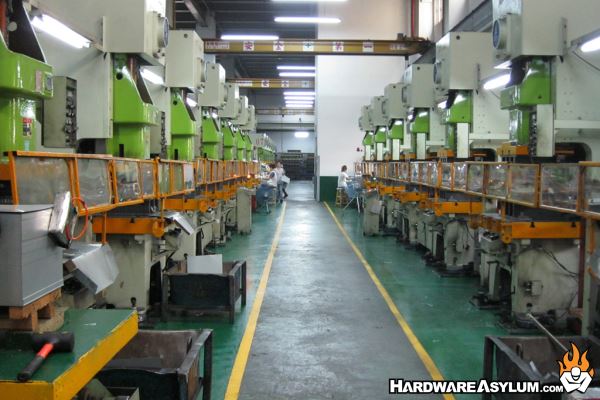
Each press is fitted with a tool that forms the metal. Some of these tools punch holes in the metal while others will shape and fold the metal as needed. These shapes aren’t realized in a single stamp but are rather built up over the course of the assembly until they reach the end. If additional work is needed the piece is stacked and moved to another station.
Once the parts are stamped and measured they move on to paint and like the stamping conveyor the parts are hung on a rack sent through the automated painting process. I know a few things about painting and I’m amazed at how efficient the painting process is both in getting a smooth finish and the lack of excessive overspray.
The parts are then sent thru a drying oven and later pulled off the rack and wrapped in protective paper for final assembly.
Final assembly is usually done with rivets but I did notice a few cases getting a spot weld or two for additional strength. The rivets are installed using a linear rivet gun that pulls the rivet in one fluid motion. A tool table is configured so that more than one rivet can be installed at once so the operator only needs to load the rivets, place the part and activate the table.
Once the case has been assembled you still need to install the front panel and writing. After that you can do a final inspection and drop the finished case into the retail packaging.
Of course there is more to a case factory than just metal bending and rivets. For In Win they create everything themselves and the metal part is only half the story. Be sure to check out the gallery of images below for more information on the various machines and processes involved in creating a computer case.